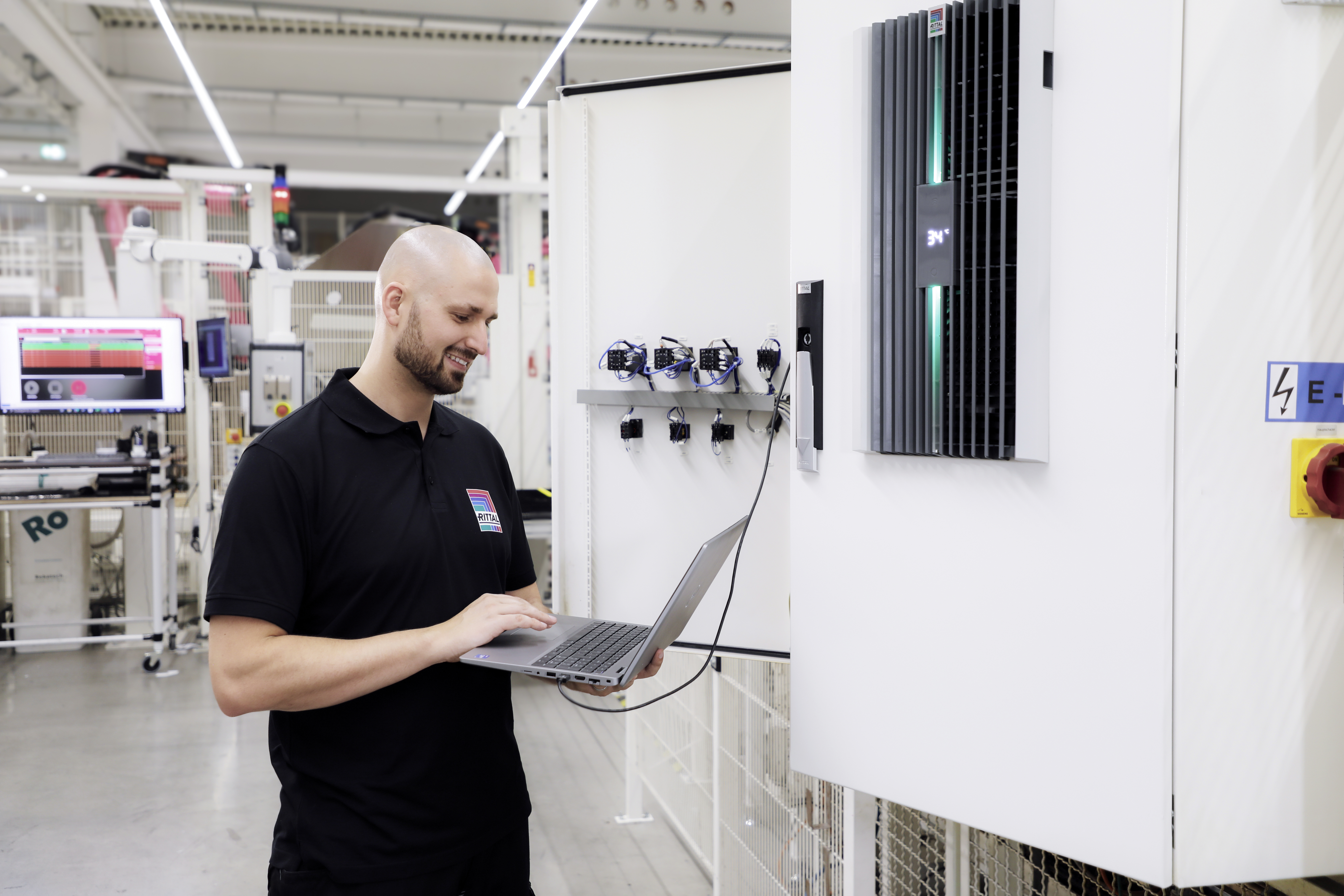
Bridging the Gap: The Role of External Service Companies
British manufacturing is grappling with significant labour and skills shortages that are so severe, they are now disrupting production lines and inflicting substantial financial damage on businesses.
Across the board, there are an estimated 70,000 vacancies affecting positions ranging from operatives to engineers. On the one hand, these labour shortages are causing operational efficiency and productivity issues; on the other, they are stifling growth and undermining businesses’ confidence to invest and expand.
The financial losses can be staggering.
In sectors like food and drink manufacturing (the UK's largest manufacturing sector), labour shortages have led to an estimated £1.4 billion loss in output over a year. These financial losses don’t just have an impact on the manufacturers, but also on their supply chains and the wider economy.
There are various reasons suggested for the recruitment crisis, ranging from an ageing sector workforce, to a worrying lack of interest in either technical education programmes, or indeed taking up a trade, among the younger generation.
One area that has been badly impacted is the service and maintenance sector, which has had a knock-on effect around the performance of critical equipment.
Maintaining Production Lines and Equipment Efficiency
A Performance in Focus Maintenance Engineering report published in 2024 by RS Integrated Supply in collaboration with the Institution of Mechanical Engineers (IMechE), highlights the main issues. They include attracting and retaining talent, which was cited as one of the major concerns – over and above any wider economic challenges, such as inflation and rising costs.
Furthermore, half the maintenance professionals surveyed believe a shortfall in available skilled labour is contributing to an increase in unscheduled downtime. The report goes on to say that it was taking maintenance teams around 15 hours per week to manage these breakdowns, at a reported cost of around £5,471.95 per hour (around £80,000 per week).
Equipment breakdowns can have far reaching consequences for manufacturers. As well as delaying order fulfilments, they can also have an impact on product quality, increase operational costs, reduce customer confidence, and diminish competitiveness.
It’s unlikely the pressures will ease any time soon, because even as manufacturers start to embrace Industry 4.0 technologies such as automation, robotics, the Internet of Things (IoT), and AI, to modernise their production processes, there is a worrying shortfall in the number of workers who can manage these systems.
These advanced technologies are often equipped with machine learning, monitoring, and analytics capabilities, which means that they support predictive maintenance strategies. However, they need skilled teams to operate, maintain and optimise them, while also being able to troubleshoot when the machines encounter unforeseen problems.
In fact, software and systems failures are routinely stated as a leading causes of production downtime, which is no surprise because factories can be hostile places for delicate IT circuitry and electrical systems.
For example, dust is a constant problem in industrial spaces that can never be fully removed. A base level of airborne particles will be present in all manufacturing facilities and this particulate matter is drawn into IT equipment enclosures by their cooling fans. It can get into wire connections and internal component fans, either blocking and shorting wiring connections, or preventing thermal exchange.
How External Service Companies Can Help
While skills shortages will inevitably lower a business’s resilience, affordable solutions are readily available.
In October 2024, leading industry magazine PWE highlighted that, “Leveraging supplier expertise and outsourcing specialist tasks may provide a valuable means of addressing both skills shortages and the demands of modern maintenance.”
In other words, in the absence of in-house expertise, a viable alternative business strategy would be subcontracting maintenance work to specialist providers.
This is exactly what we’re seeing happening in the market at the moment.
An increasing number of manufacturers are now turning to external service companies to get access to engineers who are highly skilled in predictive maintenance, IoT, data analytics, machine learning, machine operation, and in advanced support systems.
Andy McPhee, UK Service Manager at Rittal advises, “Our specialist service and maintenance teams have in-depth knowledge of our products and systems. They can perform advanced diagnostics on existing equipment, as well as put in place proactive maintenance strategies.
“We can use data analytics and IoT technologies to predict equipment failures before they occur, helping to reduce downtime and its associated costs.
“Plus, the service is extremely flexible. Manufacturers can fully outsource service and maintenance, or we can integrate into existing service and maintenance teams, bolstering team numbers and providing them with 24/7 access to a specialist, skilled team knowledge. All this is backed by tailored service level agreements for complete peace of mind.”
But the value of outsourcing doesn’t just lie in direct support and intervention to manage technology; it also extends into long-term workforce development.
Andy McPhee continues, “External partners, such as Rittal, can play a crucial role in bridging the skills gap by providing support and training to in-house teams.
“Our engineers have been trained at our Head Office in Germany - home to Rittal’s global product development, manufacturing and innovation teams.
“They can collaborate with an existing maintenance team to help enhance staff capabilities in highly specialised areas such as machine learning and AI predictive maintenance. We’ve seen how this approach can help foster an in-house culture of continuous improvement which is typically faster than manufacturers would otherwise be able to do, potentially boosting recruitment, and increasing worker satisfaction and retention levels.”
Final Thoughts
Addressing the current skills shortage in British manufacturing will require long-term investment, involving the collaboration of industry partners, educational institutions, and the government.
It’s hoped that the sector’s rapid adoption of Industry 4.0 technologies, IoT, and AI will help make the sector more attractive as a career option to younger, tech-savvy workers which will, over time, boost recruitment ratings.
But at a time when operating margins are under huge pressure, there is an urgent need for businesses to increase their efficiency levels and invest in skills development.
More needs to be done, not just to support training and apprenticeships, but also in embracing partnerships with external service and maintenance teams to cost-effectively navigate the immediate challenges of persistent production breakdowns.
Plus, as we’ve seen, such collaborations also contribute to the long-term development of a skilled and adaptable workforce, and this will be essential for the sustained success of the sector across future generations.