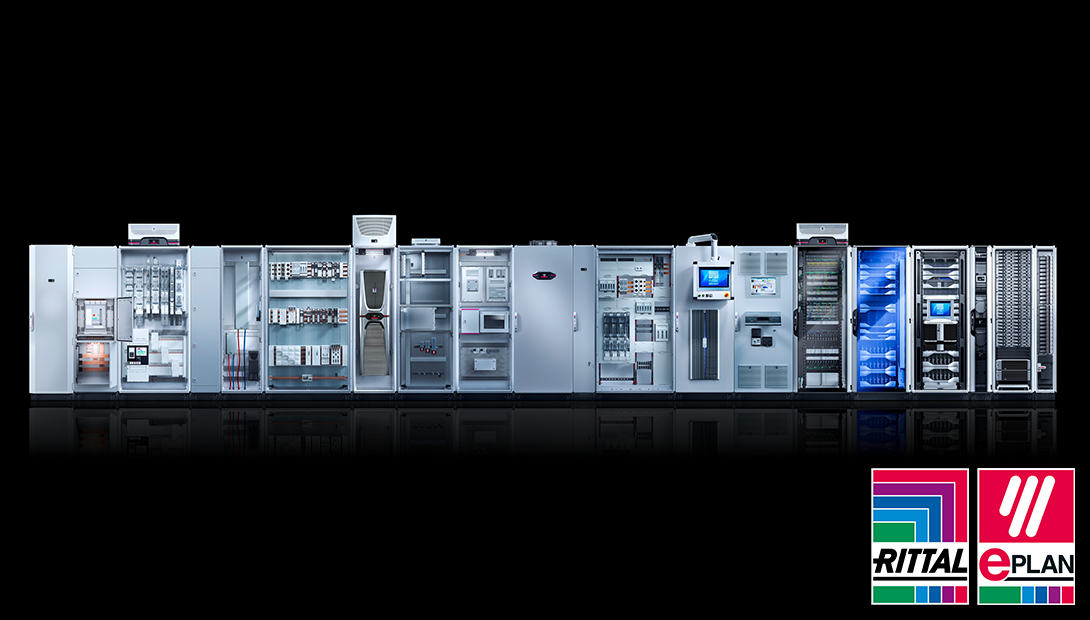
The evolution of enclosures – How Rittal technology has driven changes in equipment protection.
However, the changes and developments in design we have seen over the years may be subtle from when they first came onto the market many decades ago, since then a great deal of innovation has gone into these products that serve almost every industry.
Enclosures were initially manufactured for each specific project with fabrication companies making them in all shapes and sizes to suit the application. In the 1960’s came the first step in the evolution. In 1961 Rittal developed the concept “Enclosures off the shelf immediately.” In its founding year, Rittal launched the world’s first standard enclosure on the market, at the time a grounding breaking development within the panel building and switchgear manufacturing industry. This meant the panel builders could simply select an enclosure that best suited there needs, as opposed to waiting weeks for one that was built specifically for their project.
The first enclosures were comprised of several parts that are still around today. Since the 1960s within industry, there has been vast changes in enclosure development that are now the foundations of today’s designs.
Traditional enclosures did not have the design features we see today, since then we have become much more aware that the enclosure is there to protect the equipment inside. Within panel building and switchgear manufacturing today, many enclosures used to protect critical infrastructure that can be worth hundreds of thousands of pounds. The mindset of the end user has most definitely changed, it is now recognized as more than just a box.
Technological Developments
Changes in technology have driven many of the innovations, cable entry for instance, cables now tend to be smaller in diameter, but if we are looking at fibre or copper cables, they are also more fragile, this means when cable glanding needs to be considered, how small wires can be used, also ensuring the bend radius doesn’t damage the fibres.
Technology is changing and components we once traditionally knew, are now being packaged smaller and smaller. This means that when used in industry we have to be innovative in how we install these components within an enclosure.
Variable Speed Drives
There was a time when items such as variable speed drives, were significant in size and were traditionally mounted in floor standing enclosures. Due to progression in design and installation, Rittal is now seeing a shift towards more and more VSDs in larger wall mounted cabinets. This means we have to ensure that each enclosure is capable of taking the weight of these parts and that cable entry into the cabinet is adequate, as with all wall mounted cabinets you do not have the same access into the panel, as you would with a floor standing enclosure option.
Technological advancements in IT
Of all the areas in industry, we have seen the most change is in the provision of IT, this in turn throws up new challenges as servers have changed significantly. They have become smaller and more components can be fitted into a rack. Cable management has become an important element due to the increase in the number of connections in one rack.
Enclosure Climate Control
A higher density of equipment means more heat being generated. Technological advancements in IT climate control have made it possible to cool this type of equipment and meet the demand of the internet age and beyond.
We must also ensure that the hinges of the enclosures are sufficient to take the weight of any cooling units needed. In conjunction with the increase of equipment being installed inside the enclosure, the cooling units have to mirror this effect and increase their performance accordingly, this means the physical size and weight of the cooling units within the enclosure will continue to grow, putting more strain on the enclosures outer hardware.
As technology within enclosure design and construction has developed, so has that of the climate control that supports the equipment inside the enclosure. In the past many industries believed that air cooling was sufficient to meet their needs, but the increase in ‘high density’ computing means liquid cooling is the future, whether that is via ‘pods’ of racks being flooded with chilled air via liquid cooled equipment connected to external chillers, or even small stand alone installations where the rack, cooling and equipment are blocked off from the world. This has created their own ‘mini datacenter’ to ensure IT servers are kept in a protective environment.
Recently, many top end installations are utilizing cooling that is being physically mounted to each individual server. There are some organizations who are using more radical ‘immersion cooling’ which involves the IT equipment being submerged in electrically safe liquid to take away all heat generated.
Rittal’s thermal management tool can be applied and utilized in smaller cabinets and in enclosures containing a high density of equipment. Using the mobile application to manage the enclosure temperature, in research studies it has shown that Rittal therm software is able to increase energy efficiency by 75%. This making manufacturing operations significantly more sustainable and more cost effective.
Industry specific enclosure design
Some enclosure design is also driven by specific industries, changes in legislation can mean what was once considered fit for purpose is now no longer suitable in that environment. Let’s take the food and beverage market as an example. At one time standard enclosures were seen as sufficient, now due to changes in food hygiene regulations, the need for hygienically designed enclosures is now a necessity within a food and beverage production environment. Enclosures on production machinery need to be able to cope with the rigour of high pressure chemical washing daily. Standard design IP ratings and enclosure seals are no longer acceptable for protecting the critical equipment they are housing which ensures the smooth running of these facilities.
One thing is clear, enclosures need to be versatile and open to the changes in technology. Enclosure manufacturers need to be innovative in their ability to create solutions for customers markets or industries, where the current enclosure offering is not suitable. Rittal is aware that future technology will almost certainly keep shrinking in size and that in time, more equipment will need to be fitted into an enclosure in which the components will need to be connected.
Outdoor enclosures - the unsung heroes
As technology continues to evolve, outdoor enclosures will increasingly play a role in keeping us all connected. During the design and installation of outdoor enclosures, there are several key factors to consider, including the ability to monitor them remotely and maintaining high levels of security to prevent unauthorized access, this will remain of paramount importance, to protect the vital equipment and infrastructure, housed within many outdoor enclosures. Here at Rittal, we are able to meet the needs of many vertical markets and sectors that have specific design and legal requirements for their outdoor enclosures.
One thing that hasn’t changed since the 1960’s is the need and demand for ‘off the shelf’ solutions. This requirement is greater than it has ever been before, customers and end users across the globe want to feel confident and be able to fulfil specific projects, with specific products but they want a solution they can rely upon to be delivered quickly and efficiently.
To find out more about Rittal's full range of enclosures, follow the link to the microsite below:
To view the full range of Rittal Enclosure products and other product areas that are avaliable, download the Catalogue 36 here: