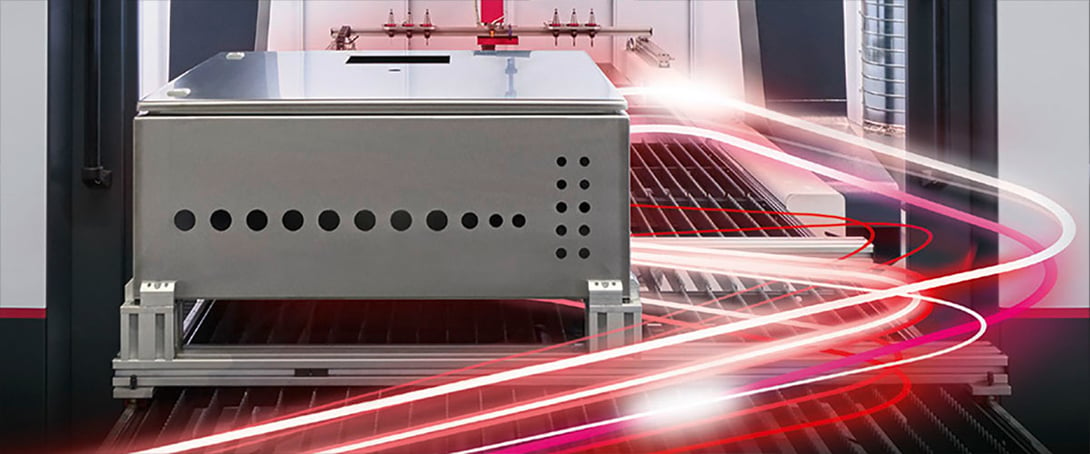
Streamline the Panel Building Process
Control and switchgear manufacturers are looking for ways to improve productivity. And they find them by leveraging the latest machining technology to increase automation in their value-creation processes. To this end, a variety of automation solutions exist that help to accelerate individual manufacturing tasks, and they can be scaled to a business’s size, and tailored to its specific imperatives. In addition to enclosure systems and software solutions, Rittal Automation Systems, the new Rittal business unit, now also provides the machining and handling technology needed for time- and cost-efficient production in the control and switchgear manufacturing business. And all from a single source. The portfolio of this business unit comprises a broad range of products, from manual tools to fully automated machining centres.
Efficient machining
To optimise the machining of panels and enclosures in the workshop and boost efficiency, Rittal supplies Perforex machining centres, which have been developed specially for control and switchgear manufacturing. These systems are used to drill holes, tap threads and perform milling work on workpieces – on an automated basis. All the materials commonly used in enclosures can be machined, such as steel, stainless steel, aluminium, copper, various plastics and other machinable materials, mounting plates, chamfered and coated doors, covers, console plates, casings and much more besides. Depending on the machine type, panels up to (WxH) 3,400 x 1,700 mm and enclosures up to (WxHxD) 2,200 x 2,300 x 2,300 mm can be clamped and fixed in place pneumatically. The tool magazine can accommodate 18 or 20 tools at the same time as standard. Up to 4 tools can be accommodated as an option.
The user interface of the Perforex system makes workshop programming easy to learn and supports remote servicing. The software is network-capable and uses a central database. All programmed workflows are thus immediately available on the machine and can be reused. Alternatively, almost all standard CAD and e-planning systems can be used for programming. Drilling data can be taken directly from Eplan Pro Panel, for example.
Fast and accurate lasering
A further key development is the new Perforex LC 3D laser centre. As its name suggests, it uses laser technology to quickly and accurately machine panels, but also entire enclosures and housings. The 3D laser technology is ideal for machining stainless steel, sheet steel and powder-coated plates such as enclosure doors, side panels, etc. Coated sheet metal parts, even with delicate contours, can also be cut without causing any noticeable damage to coatings or discolouration. What’s more there is no blooming at cut edges when machining stainless steel. Perforex LC 3015 is cost-effective when machining just 150 stainless steel enclosures or 300 sheet steel enclosures per year. It machines stainless steel twenty times faster than conventional milling processes and can process five enclosure surfaces simultaneously in a non-contact, low-vibration manufacturing process. The laser centre also features user-friendly workshop programming, has interfaces for Eplan Pro Panel and gives users the option of processing the neutral DXF format.
Fast and accurate cutting
The manufacturer also supplies the Secarex cutting centre, which is designed to cut cable ducts, cable duct covers and support rails to size quickly, accurately and safely. Thanks to the automatic length stop and cut visualisation with laser pointers, it is now possible for protracted and complex measuring processes, inaccurate cutting and complex handling to be consigned to the past. High-performance tools deliver better quality, optimised waste quotas, lower costs and a faster overall process.
Flexible assembly
The Athex automatic assembly machine takes care of the time-consuming process of assembling and labelling terminals. The terminal placement machine is a flexible, universal solution for the automated manufacture of terminal blocks for control system engineering. Athex prints and labels terminals according to a CAD template or manual configuration onto the support rails. The terminal magazines can be changed and topped up while the machine is operational and can accommodate various terminal types from all popular manufacturers. There is also the option of carrying out labelling during placement using an laser printer. An integrated cutting centre feeds support rails out of a magazine and into the delivery unit, cuts them to the right length and labels them.
Simple wiring
Wiring all the components in an enclosure is a complex process that is prone to errors. Rittal Automation Systems is tackling this problem head on and offers “Smart Wiring”, a solution provided by Rittal’s sister company Eplan. This new software tool is used to provide production systems with all the information needed for wiring such as wiring routes, etc. It also visualises this data. Users save a great deal of time compared to manual wiring. And for the first time, Rittal’s offering now includes a crimping machine for cutting and assembling cables. For the very highest level of wiring, Rittal offers the fully automatic Averex wiring robot for large-series production. The robot shows how the time-consuming manual wiring of mounting plates can be replaced with fully automated wiring in line with applicable standards and safety requirements.
End-to-end data
End-to-end digital workflows and data are the key to completing control system and switchgear manufacturing processes cost-effectively and at maximum speed. At the heart of the digital workflow is the virtual prototype of the planned system, which seamlessly interconnects all process steps from design engineering through to automated production. By establishing the new Rittal Automation Systems business unit, Rittal is responding to the trend in control system and switchgear engineering for ever-closer integration between processes from design engineering through to production. Together with Eplan, the company has developed value-creation solutions that ensure data can flow freely throughout the entire production cycle.
Do you want to discover more? Mark Guest, Product Manager for Industrial & IT Power discusses how industrial companies can add value to their processes and make them faster, more economical and more precise in this recorded webcast.