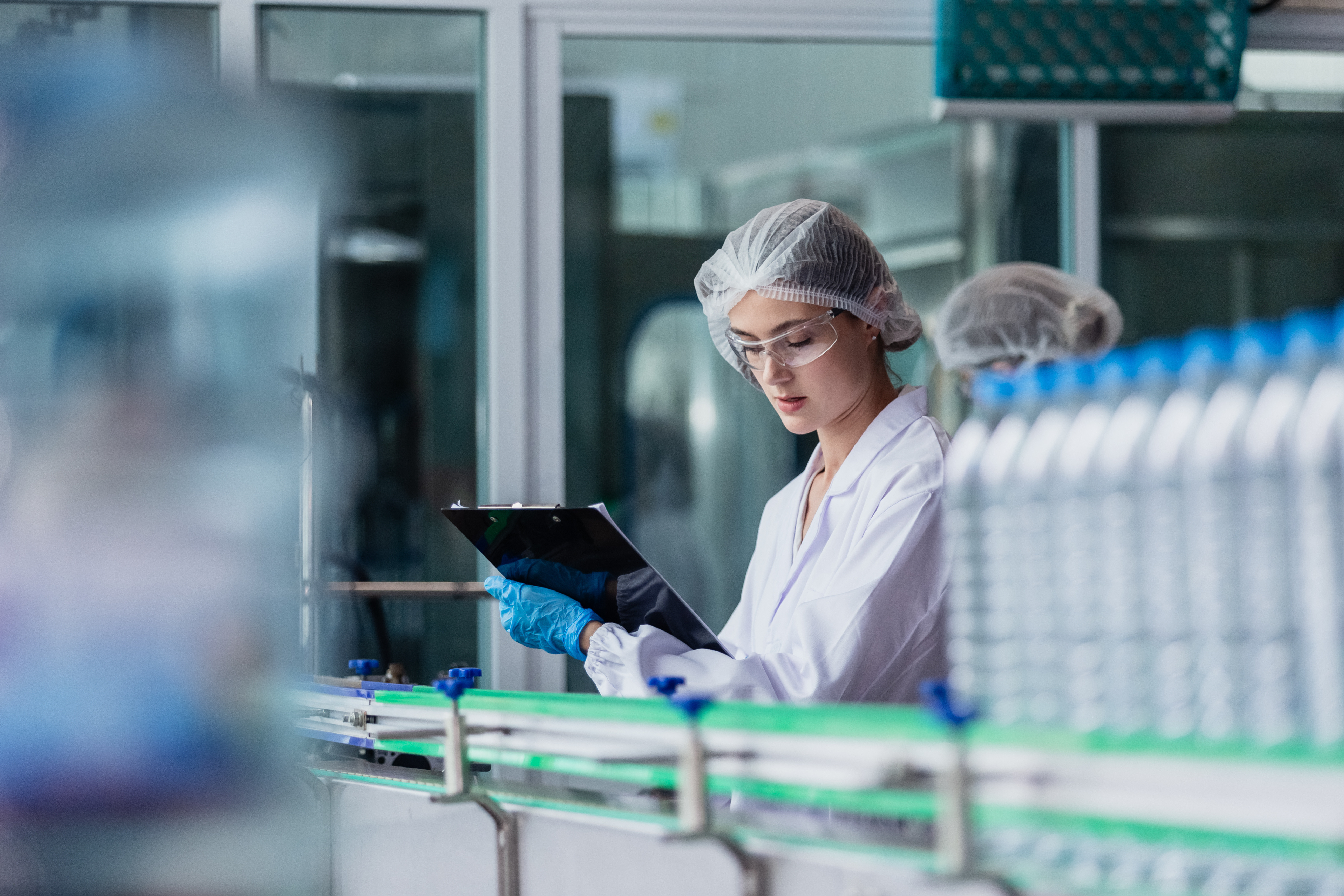
What Does Rittal Do: Food and Beverage Industry
Introduction
The food and beverage industry operates under some of the strictest hygiene and safety regulations, making the protection of electrical components a unique challenge. Factors like high-pressure washdowns, extreme temperatures, and corrosive cleaning agents can compromise enclosures, leading to equipment failure, costly downtime, and even product contamination.
Here at Rittal, we understand these challenges and provides tailored solutions to ensure that electrical systems remain secure, operational, and compliant. From site assessments to long-term standardization strategies, we help manufacturers safeguard their operations with enclosures designed specifically for food and beverage environments.
Rittal in Industry: An Overview
Rittal’s main goal is to ensure that electrical components are protected and housed appropriately across a wide range of applications. Food & Beverage manufacturing by its nature makes this a unique challenge due to strict hygiene requirements, washdown, high temperature processes and potentially aggressive conditions, either from byproducts or from chemicals used in cleaning.
When these challenging conditions are not properly addressed from the outset by using appropriately designed enclosures and panel coolers, the result can become overheating control panels, water ingress, dust ingress, and corrosion. These consequences can then trigger a cycle of downtime, rushed repairs, or worse yet; potential product contamination.
Rittal helps Food & Beverage manufacturers break this cycle. We begin with a site visit to understand your current setup and the challenges you face. Next, we address pressing short-term issues with retrofit solutions whenever possible. One example is overheating control panels, which are a common cause of downtime. Rittal solves this by assessing the affected panels, performing thermal calculations, and retrofitting appropriately sized panel coolers to help prevent the issue from recurring.
In the long term, Rittal helps Food & Beverage manufacturers develop strategies to prevent recurring issues. After gaining a thorough understanding of your site, we collaborate with you to create or refine site standards, ensuring that your unique site conditions are addressed and appropriate solutions are specified. This ensures that future expansions or upgrades are designed to meet the specific challenges of each area of your site. By proactively including these considerations in your standards, we help maintain reliable operations, reduce downtime, and eliminate repeat issues.
Considerations for F&B Environments
Enclosures are imperative in creating a protective environment for sensitive electrical components. As aforementioned, with food production lines, enclosures must simultaneously protect the electrical components while also meeting strict hygiene requirements.
The hygiene regulations that govern our food and beverage production are strict for good reason in order to protect public health. Any breaches of these regulations can be very expensive for a manufacturer, leading to massive costs from product recall, production downtime, as well as potential fines and reputational damages.
Despite the strict regulations, there isn’t one clear industry standard of what defines a successful food and beverage enclosure. Therefore, the factory management team usually uses their own judgement to assess which type of enclosure should be used.
Decision-makers therefore need to assess several factors when choosing enclosures, including:
- IP ratings
- Materials and surfaces that can be easily cleaned without corrosion
- Robust connection systems, like seals and seams
- Angles and corners designed for simple washdowns while avoiding contaminants
- Protection of the circuitry from water ingress and contaminants
Most enclosures are selected based on their IP rating. While this may suffice for other industries, a high IP rating is not the most important factor for enclosures residing in food and beverage manufacturing plants.
In fact, standard enclosure design makes deep cleaning almost impossible, thanks to features such as hinges, door locks, cable glands and plinths, all of which have areas where foodstuff can congregate, which in turn will become a breeding ground for microbes.
Hygienic Design Enclosures
Rittal has simplified the tedious decision-making process by creating an enclosure specifically designed for the food and beverage environment.
Our hygienic design enclosures allow for the easy yet thorough deep cleaning of an enclosure. Any dead spaces, undercuts, or joints without radius have been removed to prevent product residue from settling. Corners and joints are smooth, gapless, and cleanly rounded.
Furthermore, there are no recesses including uncovered screw threads, screw heads with internal hexagons, or Torx screws. Wall brackets are also round and smooth, and the doors with sloping upper edges prevent water pooling in them and eroding their seals.
Stainless steel as the construction material is an excellent choice since it offers high resistance to chemicals, cleaning agents, and disinfections; all key considerations within a production line.
High-intensity jets of hot water for cleaning need to run-off the surfaces of the enclosures in the spray and wet zones, which means providing appropriately angled drain slopes. A sloping roof to the enclosure allows water to run off while also allowing for easy inspection and avoiding anyone placing objects on top of the enclosure.
Closing Thoughts
To continue building upon the question of ‘What Does Rittal Do’, we have explored the food and beverage industry as an application of our business.
For highly regulated environments like the food and beverage industry, standard enclosures simply aren’t enough. Our Hygienic Design Enclosures provide a purpose-built solution to withstand aggressive cleaning procedures while preventing contamination, with considerations also made to ensure longevity and cost-efficiency.
By proactively selecting the right enclosures and cooling solutions, factory manufacturers can reduce downtime, improve compliance, and protect their production lines. Investing in the right infrastructure is the best way to future-proof your operations and avoid those dreaded costly repairs.
Want to hear more about what we do here at Rittal?
Stay in the loop with our recurring blog series, ‘What Does Rittal Do’, where we will continue to explore all facets of our company.