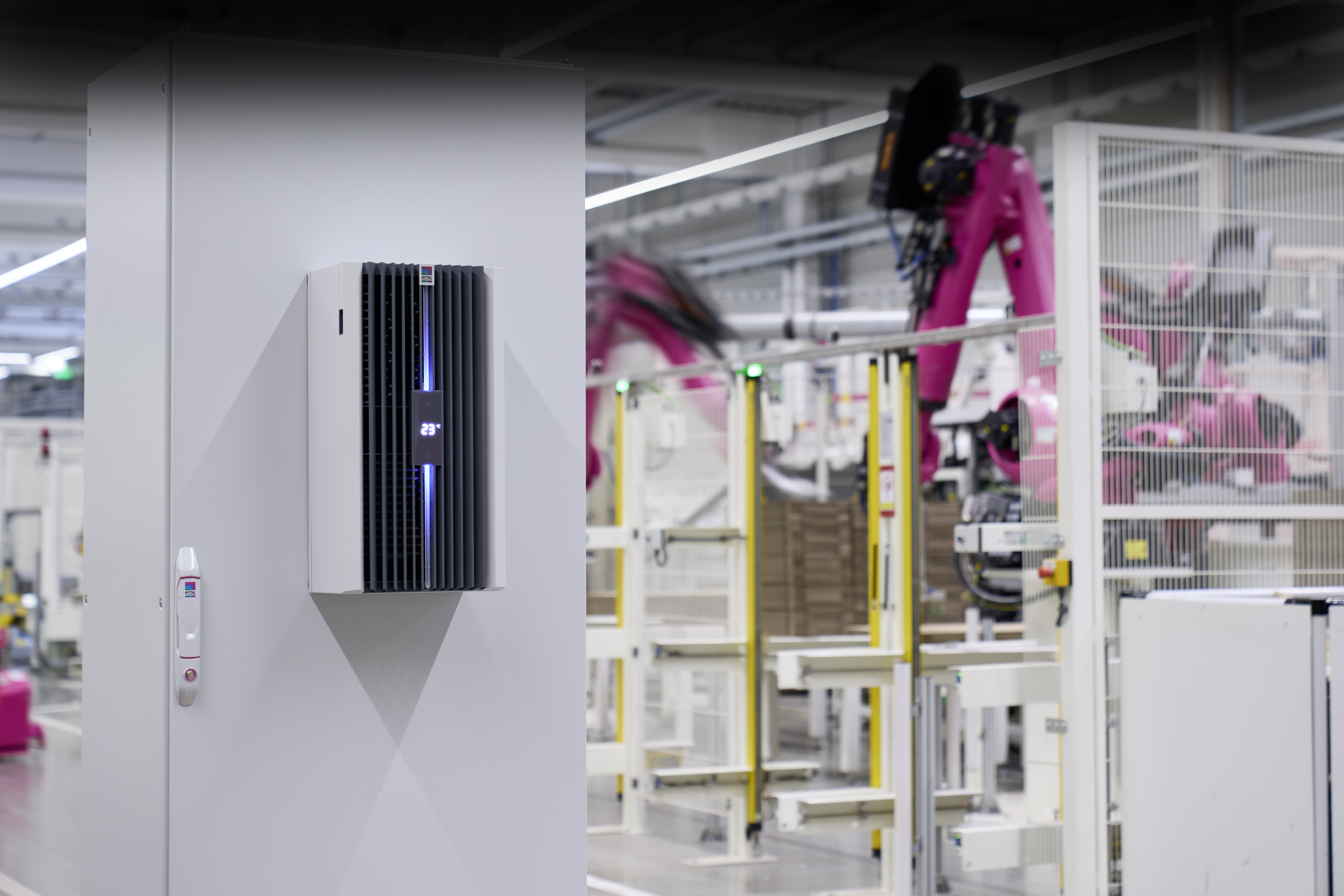
Maintaining Electrical Enclosure Cooling Units
As technology advances and industries rely more on sophisticated electrical systems, maintaining the health and efficiency of electrical enclosures has never been more critical. These enclosures house sensitive equipment like PLCs, drives, and other electronics that keep your production lines running. One of the most important aspects of maintaining these systems is ensuring that they are adequately cooled. Overheating can lead to costly breakdowns, production delays, and even permanent damage to vital equipment.
Why Cooling Matters
Electrical enclosures are designed to protect sensitive components from external elements like dust, moisture, and physical damage. However, they also trap heat generated by the equipment inside. Without proper cooling, the temperature within these enclosures can rise quickly, leading to a host of problems. High temperatures can degrade components, cause malfunctions, and significantly reduce the lifespan of your equipment. In fact, studies have shown that every 10°C increase in temperature can halve the life expectancy of electronic components.
Choosing the Right Cooling Method
There are several methods available for cooling electrical enclosures, and choosing the right one depends on the specific needs of your operation. Here are a few common options:
-
Natural Ventilation: This method relies on natural air circulation to dissipate heat. It's suitable for environments where the ambient temperature is low and the heat load is minimal. However, it's not ideal for more demanding applications, as it doesn't provide precise control over the enclosure's internal temperature.
-
Forced Air Cooling: Fans are used to circulate air through the enclosure, providing more effective cooling than natural ventilation. This method is often used in conjunction with air filters to keep dust and other contaminants out. It's a good option for moderate heat loads and environments where air quality can be controlled.
-
Air Conditioners: For high heat loads or environments where precise temperature control is essential, dedicated air conditioning units can be installed. These units provide powerful cooling and can maintain a consistent temperature, making them ideal for protecting sensitive equipment in harsh conditions.
-
Heat Exchangers: These systems use a fluid (often water or a refrigerant) to transfer heat away from the enclosure. Heat exchangers are highly efficient and are commonly used in industrial settings where space is limited, and the heat load is substantial.
Signs Your Cooling System Needs Attention
Even with the best cooling systems in place, regular maintenance is essential to ensure they operate efficiently. Here are some signs that your cooling system may require attention:
-
Inconsistent Temperatures: If the temperature inside your enclosures fluctuates or doesn't remain within the recommended range, it could indicate a problem with your cooling system.
-
Frequent Equipment Failures: Equipment that frequently trips or malfunctions may be a sign that it's overheating. This could be due to inadequate cooling or a failing cooling system.
-
Visible Dust or Debris: If you notice dust or debris inside your enclosure, it could mean that filters need replacing, or there are leaks in the enclosure that are allowing contaminants to enter.
-
Unusual Noises: Strange noises coming from fans, air conditioners, or heat exchangers can indicate mechanical issues that need to be addressed.
Preventative Maintenance is Key
To avoid the costly consequences of overheating, it’s crucial to implement a regular maintenance schedule for your cooling systems. This includes:
-
Routine Inspections: Regularly check for signs of wear and tear, such as damaged seals, clogged filters, or unusual noises. Addressing these issues early can prevent more significant problems down the line.
-
Cleaning and Replacing Filters: Ensure that air filters are clean and replace them as needed. This will help maintain airflow and prevent contaminants from entering the enclosure.
-
Testing Temperature Controls: Periodically test your temperature controls to ensure they are functioning correctly and maintaining the desired setpoint.
-
Monitoring System Performance: Use monitoring systems to keep track of the temperature and performance of your cooling systems. This can provide early warning signs of potential issues.
The Bottom Line
Proper cooling is essential for the longevity and reliability of your electrical enclosures. By choosing the right cooling method and maintaining your systems regularly, you can prevent costly downtime, extend the life of your equipment, and ensure that your production lines continue running smoothly. Don’t wait until a failure occurs—take proactive steps today to safeguard your electrical systems from the damaging effects of overheating.
For more information on electrical enclosure cooling solutions, or to schedule a consultation, visit www.rittal.co.uk, contact our customer service team at 01709 704000, or email us at cooling@rittal.co.uk.
Alternatively, book your free Rittal RiAssure cooling review using the form below.